Energy Effieciency On Dairy Units
Rising energy costs and environmental concerns are causing dairy farmers to alter their management practices. This publication by ATTRA provides an overview of how dairy farms can implement efficiency improvements and energy-saving technologies that can reduce energy consumption and energy-related costs.Introduction
Dairy farms today face challenges and opportunities fueled by rapidly rising energy costs and concerns about environmental impacts. Dairy farms use more energy than almost any other agricultural operation. Energy is used in the milking process, and for cooling and storing milk, heating water, lighting and ventilation. Determining the best energy efficiency and energy management opportunities for dairy farms will help reduce energy costs, enhance environmental quality and increase productivity and profitability.
Energy efficiency is often an inexpensive, quick and simple way to save money. This publication focuses on dairy equipment upgrades, new technologies and management practices for reducing energy consumption. Opportunities for cost savings and improved processes include the implementation of: variable speed drives for milk vacuum pumps and milk transfer systems, plate pre-coolers, heat recovery systems, energy-efficient light fixtures and efficient ventilation systems. Information on energy audits, financial incentives and further resources is included. The opportunities presented in this publication were developed for cow dairies but may be applicable to goat and sheep dairies as well.
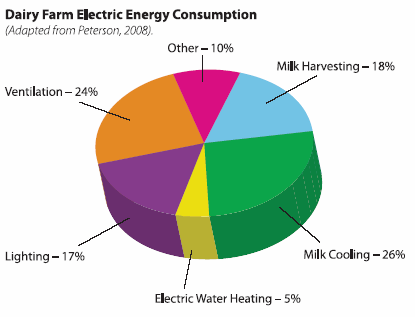
Milking process
The milking process consists of harvesting milk from the dairy cow and transporting the milk to a bulk tank for storage. Th is process can take place one or two or more times per day and most dairies schedule their lactations for a continuous milk supply throughout the year. On average, milking utilises 18 per cent of the electrical energy use on a dairy farm (Peterson, 2008).
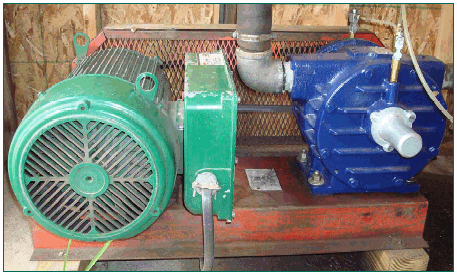
Vacuum pumps
The vacuum pump operates during the milk harvest and equipment washing and can consume 20 per cent to 25 per cent of all electrical energy use on a dairy farm. The vacuum pump creates negative air pressure that draws milk from the cow and assists in the milk flow from the milk receiver to either the bulk tank or the receiver bowl. The airflow also sends water and cleaning agents through the milking system during the washing process.
There are four main types of vacuum pumps: sliding vane rotary pumps, watering pumps, rotary lobe (blower) pumps and turbine pumps. Each of these operates and uses energy differently. Vacuum pumps become less efficient as the vacuum level increases (Ludington et al., 2004). Therefore, operating the vacuum pump at lower vacuum levels conserves energy.
Sizing the vacuum pump to meet the needs of the milking and washing system can reduce capital costs for equipment, reduce energy operating costs during the life cycle of the pump and ensure that the pump is performing properly. The size of the vacuum pump is dependent on all of the components in the system that admit air during operation. Pumps are generally sized by accounting for the amount of air admitted into the milking system during the milk harvest plus a 50 per cent reserve to account for accidental air admittance and the wear and tear of parts (MMMC, 1993). Outdated industry standards used to recommend oversized vacuum pumps in part because of an incorrect belief that additional vacuum capacity is necessary for washing. An oversized vacuum pump may overheat as the pump ends its cycle. The current industry performance standard, ASAE Standard S518.2 Feb03, Milking Machine Installations, provides current sizing guidelines for dairy vacuum pumps (Ludington et al., 2004).
Variable-speed drives
A variable-speed drive (VSD), also referred to as an adjustable-speed drive or variable frequency drive, is an energy-efficient technology used for controlling the vacuum level on sliding-vane rotary pumps and rotary lobe pumps. Traditional vacuum systems run at maximum speed only, and rely on a vacuum regulator to vent excess air that is not being used during milking or washing operations. A VSD adjusts the speed of the pump motor to meet the vacuum demand so that equal amounts of air are being removed by the vacuum pump and entering the milking system. By eliminating the amount of air that would be admitted through a regulator, the motor uses less horsepower during most of the milking process. A VSD on a vacuum pump eliminates the need for a conventional regulator because less energy is delivered to the motor and its operating speeds are reduced. Energy operating costs of a vacuum system with a VSD can be reduced by up to 60 per cent (Ludington et al., 2004). In addition, lowering the vacuum pump’s RPMs can extend its life as there will be less wear and maintenance costs.
Vacuum pump maintenance
Following the manufacturer’s maintenance schedule, along with routine maintenance on all vacuum pump systems, can save energy. Checking the temperature of the vacuum pump near the end of each milking is a good way to detect problems with the pump or electrical load. High motor temperatures may indicate the need for a vacuum adjustment, removal of exhaust restrictions, repair of rotary vane oiling systems or cleaning lobe blower pumps. Changes in the speed of the vacuum pump can be caused by air leaks in the milking system, degraded drain seals, loose pump belts, malfunctioning pulsators or a malfunctioning VSD vacuum sensor. A 5-cubic-foot-per-minute air leak in the vacuum system can amount to over $100 in wasted electrical costs (Peterson, 2008). Problems associated with vacuum pumps can be avoided by regularly checking vacuum levels and the operation of the VSD.
Milk cooling systems
Cooling milk accounts for most of the electrical energy consumption on a dairy farm. Milk is harvested from a cow at around 95 to 99 degrees Fahrenheit (F). To maintain high milk quality, including low bacteria counts, the raw milk temperature needs to be lowered quickly to around 38 degrees. Refrigeration systems consist of a bulk tank, a motor-driven compressor unit, an evaporator and a condenser unit. The system operates by pumping a refrigeration coolant in a cycle that gives off heat as it condenses. Heat exchangers cooled by well water, variable speed drives on the milk pump, refrigeration heat recovery units and scroll compressors are all energy conservation technologies that can reduce the energy consumed in the cooling system.
There are two types of milk cooling systems used on dairy farms. A direct expansion cooling system cools the milk directly in the bulk tank by using evaporator plates that expand in the lower portion of the tank. Indirect, or instant, cooling systems rely on heat exchangers to pre-cool the milk before it enters the bulk tank. A pre-cooling heat exchanger can lower milk temperatures as much as 40 degrees, resulting in refrigeration energy reductions of about 60 per cent (Sanford, 2003b).
Heat exchangers
Heat exchangers used for pre-cooling raw milk transfer the heat from the milk to an intermediate cooling fluid, such as well water or a water-glycol solution, by having the milk and coolant flow in concurrent or counterflow configurations. In a concurrent flow configuration, the milk and coolant flow in the same direction. The fluids flow in opposite directions in a counterflow pattern. Counterflow systems allow for lower milk temperatures. The amount of cooling that takes place depends on the flow of the milk in relation to the flow of the coolant, in addition to the heat transfer area, the number of times the milk passes through the coolant and the temperature of the coolant. Well-water heat exchangers have been implemented in pre-cooling systems for more than 20 years and can reduce cooling costs by 0.2 to 0.3 kWh/cwt (hundred weight of milk) (Ludington et al., 2004). There are two types of heat exchangers used for pre-cooling: shell-and-tube heat exchangers and plate heat exchangers. Shell-and-tube heat exchangers consist of a single small tube or multiple small tubes inside of a larger tube. The milk flows through the smaller tube(s) while the well water flows through the larger tube. Plate heat exchangers are made up of a series of metal plates that are located side by side. Milk and well water run in opposite flow channels and the well water absorbs the heat from the milk on the opposite side of each plate. Plate heat exchangers are relatively small in size and, unlike shell-and tube heat exchangers, additional plates can be added to increase capacity.
Heat exchangers are designed so that the milk and coolant make single or multiple passes between the plates or tubes. In a single- pass heat exchanger, a circuit is arranged so that the two fluids are in contact as they go through separate sets of plates or tubes before exiting the heat exchanger. Multiple- pass heat exchangers route the milk and coolant flow through two or more circuits, putting the milk channels in contact with the coolant channels for longer periods of time. A heat exchanger can be designed so the milk travels through multiple circuits and the coolant flows through a single pass, or circuit. Farms that milk for long periods of time can use heat exchangers that are designed for two coolants. The use of two different cooling fluids, such as first pre-cooling with well water and then with chilled water or a glycol-water solution, can cool the milk as it is harvested.
pre-cooler energy savings
Installing a properly sized pre-cooler can reduce refrigeration energy consumption by about 60 percent (Sanford, 2003b). A properly sized well water heat exchanger can reduce milk temperatures to within 5 to 10 degrees of the groundwater temperature. Higher efficiency for pre-cooling can be achieved with a 1-1 ratio of coolant to milk flow and by using the largest water lines possible in order to maximise the coolant flow. Other factors that determine the energy and economic savings of a pre-cooler include herd size, number and size of compressors, type of coolant used and the age of the bulk tank. An added benefit of using water for pre-cooling is that it can afterwards be used for livestock drinking water. Cows depend on drinking water to produce milk and prefer warm water to cold. The warm water can also be used to perform other tasks, such as washing and heating.
Variable-speed milk pumps
As previously stated, a vacuum is required to harvest milk. The milk, however, cannot transfer from a pipeline that is under a vacuum to a bulk tank that is at normal atmospheric pressure. To compensate for the difference in pressure, milk can flow into a receiver bowl that triggers a milk transfer pump to push the milk from the receiver bowl either through a heat exchanger or directly into the bulk tank. Another option that eliminates the receiver bowl and milk transfer pump requires putting the bulk tank under a vacuum by placing rubber seals on the bulk tank covers.
A variable-speed milk transfer pump can further reduce energy use by slowing the flow rate of milk through the heat exchanger. A lower and more continuous milk flow rate through the heat exchanger increases the coolant-to-milk ratio and results in greater milk cooling. Milk can be cooled by an additional 15 to 20 degrees by installing a variable-speed milk transfer pump (Sanford, 2004c).
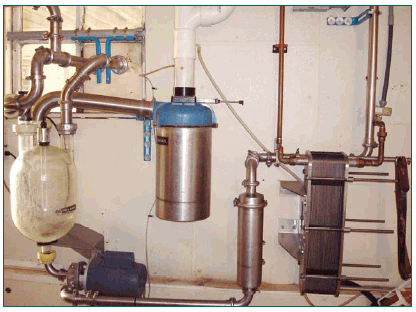
Refrigeration heat recovery units
Refrigeration heat recovery units (RHR) capture the waste refrigeration heat from the condenser to preheat water before it is transferred to a water heater. An RHR unit can recover 20 to 60 per cent of the energy that is required to cool milk for storage (Sanford, 2004b). Depending on the number of cows being milked, the RHR storage tank should be sized to provide enough hot water for one milking. Th is includes hot water for washing the milking system and for washing the bulk tank. The payback for purchasing an RHR unit depends on the savings from heating water and will vary greatly from farm to farm.
Types of refrigeration heat recovery units
There are two types of RHR units: desuperheating and fully condensing units. A desuperheating unit operates only when the refrigeration system operates and produces water temperatures around 95 to 115 degrees (Ludington et al., 2004). These units can be inexpensive to add, but only part of the available heat can be transferred to the water. Nearly all of the available refrigeration heat is recovered as hot water from a fully condensing unit, with temperatures reaching 120 to 140 degrees (Ludington et al., 2004). Th is type of RHR unit meets the requirements of the cooling system by using a valve to control the flow of cold water through the heat exchanger. Once the storage tank is full, excess warm water can continue to be used and not wasted. A fully condensing RHR unit replaces the need for a regular condenser in the refrigeration system and is best integrated as part of a new or replacement refrigeration system. If nearly all of the energy captured by the RHR unit is used for preheating water, then a pre-cooler is not needed to remove heat from the milk and may, in fact, increase overall energy costs.
Compressors
The function of a compressor is to compress the cold, low-pressure refrigerant gas from the evaporator to a high-pressure, high-temperature state for condensing. The three types of refrigeration compressors used for milk cooling on dairy farms are the reciprocating, scroll and discus. The reciprocating compressor is the most common and can be either open type, hermetic or accessible hermetic. The scroll and discus compressors are newer and more efficient than reciprocating compressors. Research has shown that replacing a failed reciprocating compressor with a new scroll compressor can reduce milk cooling costs by 20 per cent because of a reduction in the electrical demand (Ludington et al., 2004).
Heating water
Hot water is essential for producing high-quality milk on dairy farms and is primarily used for cleaning milking systems. The amount of hot water required varies from farm to farm and depends on the size of the milking herd and the type and size of the milking system. On average, a minimum of 4 gallons of water at 170 degrees are required for each milking unit (Ludington et al., 2004). Hot water is generally produced by water heaters that use either fuel oil, natural or propane gas, solar energy or electricity. For some dairy farms, heating water can account for about 25 per cent of the total energy used on the farm (Sanford, 2003a).
Types of water heaters
There are several ways to reduce the amount of energy used for heating water. Whether using a direct or indirect water heater, overall efficiency is determined by the combustion efficiency of the fuel source and the amount of heat loss from the storage tank, known as standby loss. A direct water heater combines the water storage tank and the heating element. The storage tank in an indirect water heater contains a heat exchanger that is connected to a separate boiler unit. Insulating the storage tank and connecting pipes can reduce standby losses for both types of water heaters. The sides and top of an electric water heater and the sides of gas and oil water heaters can be insulated.
Water temperatures
Proper water temperatures are essential for cleaning milking equipment. Using warm or cold water when possible can help reduce energy costs. A warm-water pre-rinse, about 95 to 110 degrees, does not cause the milk to stick to the equipment, which is a problem with cold water. Additionally, a warm water rinse does not cause mineral and protein deposits in the pipeline, as is often the case when using hot water. The wash cycle requires water temperatures between 120 and 170 degrees. Dairy farms require the use of commercial water heaters since residential electric water heaters are thermostatically controlled not to go above 140 degrees because of federal safety regulations. The thermostat range for commercial water heaters is 100 to 180 degrees. A cold acid rinse will control mineral and bacterial buildup in the milk lines and will help conserve hot water. There are many types of dairy acid sanitisers and each one may have different rinse instructions. Most of these sanitisers are not listed on the National List of Allowed and Prohibited Substances for use in certified organic production and processing (National Organic Program) but some may be permitted for use on organic dairies (USDA, 2000). Check with your organic certifier to see if they have any restrictions for use of dairy acid sanitisers.
Electric control devices and peak demands
Using a control device for electric water heaters can reduce electricity use during periods of expected increases in demand above the average supply level, also known as peak demand. Time clocks provide a simple and cost-effective way to control water heaters. Shifting electrical loads to off -peak or low demand hours and off -peak utility rates not only ensures farmers of having hot water at a reasonable cost, but also benefits the utility provider by allowing direct control of the energy demand on their system. Many utility companies offer incentive rates or rebates to encourage farmers to participate in electric water heater control programs. Not all utility companies offer off -peak utility rates, so it is best to check with local service providers to see if off -peak rates are available.
Lighting
Appropriate lighting can improve productivity and safety on a dairy farm. On average, lighting represents 17 per cent of total dairy farm electrical energy use (Peterson, 2008). Optimal lighting conditions may increase milk productivity and conserve energy consumption. Factors that contribute to increased milk production include the type of light, the amount of light provided per watt, the temperature of the work area, the height of the ceilings and the length of the lighting period.
Lighting requirements on a dairy farm can be divided into three categories. The first category is visually intensive task lighting, which requires the highest lighting levels (Ludington et al., 2004). Areas that benefit from this type of lighting include milking parlors; equipment washing, equipment maintenance and repair areas; offices; maternity and veterinary treatment areas; and utility rooms. The second category includes lighting for holding areas, feeding areas, animal sorting and observation and general cleanup. These areas and tasks require high to moderate lighting levels. Finally, low to moderate lighting levels are adequate for general lighting for livestock resting areas, passageway lighting, general room lighting and indoor and outdoor security lighting.
Lamp types
There are three types of lighting systems used on dairy farms: incandescent lamps, fluorescent lamps and high-intensity discharge lamps.
Incandescent lamps
Incandescent lamps are common on many dairy farms, although today they are considered to be an inefficient light source. Their light output is only 10 percent, with the remaining 90 percent of energy given off as heat (Hiatt, 2008).
Lamp Type Comparison Chart
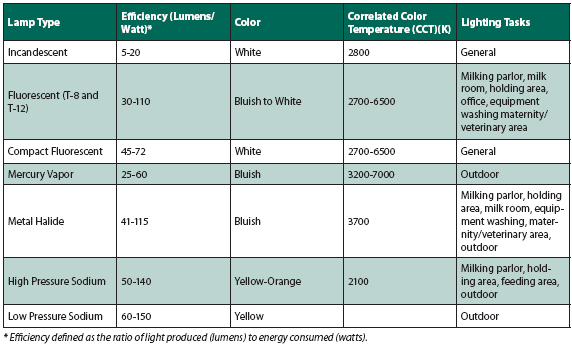
Fluorescent lights
Fluorescent lights are made of a frame, ballast, light socket and the lamp(s). Ballasts provide the needed voltage, current and waveform for starting and operating fluorescent and high intensity discharge lamps. The lamps are available in many different lengths and diameters, shapes, color temperature ratings and minimum operating temperature ranges. Fluorescent lamps range in length from 6 to 96 inches long. The diameter of the lamp is expressed in eighths of an inch and lamps come in the following diameters: T-5, T-6, T-8, T-9, T-10, T-12, and T-17. A T-12 lamp is 12/8 inch, or 1.5 inches, in diameter, while a T-8 is 8/8 inch, or 1 inch in diameter (Sanford, 2004a).
Fluorescent lamps are linear (straight), circular or U-shaped. The colour temperature index, or CCT, refers to the colour appearance of the light emitted by a lamp (Sanford, 2004a). It is indicated in degrees Kelvin (K). Lower temperature values produce a red or orange color and refer to a warm emitted light. Higher temperature values produce a blue, or cool, light source. The CCT values for fluorescent lamps range from 3,000 to 5,000 degrees K, while the average CCT value of an incandescent lamp is around 2,800 degrees K. Minimum operating temperatures for fluorescent lamps are between –20 and 50 degrees Fahrenheit, depending on whether the ballast is electromagnetic or the more energy-efficient electric type.
The most common type of fluorescent lamp is the T-12. However, smaller diameter lamps provide more light for a watt of power. Compared to a T-12 lamp and ballast, the T-8 fluorescent lamp provides about 15 per cent more light, or lumens, and the ballasts are 40 per cent more efficient (Sanford, 2004a). The most energy-efficient fluorescent lamp is the T-5, but that lamp tends to produce too much heat in an enclosed fixture. Enclosing fixtures in agriculture lighting systems protects the housing from corrosion and protects the lamp from dust, humidity and manure gases, all of which can shorten the life of a lamp.
Compact fluorescent lamps
A compact fluorescent lamp (CFL) uses about 75 per cent less energy, measured in watts, for the same amount of light as an incandescent bulb. CFLs are directly interchangeable with incandescent lamps, so changing a 60-watt incandescent lamp to a 20-watt CFL cuts energy use by one third. CFLs also last six to 10 times longer than incandescent light sources (Sanford, 2004a). CFLs can be used outdoors, but should be covered to protect the lamps from all weather conditions. Low temperatures, both indoors and outdoors, may reduce light levels. In order to reach full output at cooler temperatures, CFLs require a warm-up period.
Factors affecting lamp life
Several factors can shorten the life of a lamp. These include:
- Level of manure gases
- Humidity
- Dust
- Frequent switching on and off
High-intensity discharge lights
High intensity discharge (HID) lamps are a very bright and efficient light source. HID lamps often require a warm-up period and generate light by heating a gas mixture in the lamp. HID lamps must be mounted high in order to spread the light and to avoid a glare. Some HID fixtures can be equipped with a diffuser that distributes the light horizontally. The four common types of HID lights are mercury vapor, metal halide, high-pressure sodium and low-pressure sodium.
Mercury vapor lamps
Mercury vapor lamps emit a favorable bluewhite color that mimics daylight. However, mercury vapor lamps are the least efficient of the HID lamps, emitting only 32 lumens for a watt. In addition, their disposal poses an environmental risk due to the mercury gas.
Metal halide lamps
Metal halide HID lamps provide the best color of all the HID lamps and emit about 60 lumens a watt, making them twice as efficient as a mercury vapor lamp. A newer pulse-start lamp technology is available for metal halide lamps. The pulse-start system can extend lamp life by half over the standard metal halide lamp, provide about 8 per cent more lumens per watt and allow for faster warmups and restarts (Sanford, 2004a). Pulse-start metal halide lamps use a different type of ballast and are not interchangeable with standard metal halide lamps.
High- and low-pressure sodium lamps
Slightly more efficient than metal halide lamps are high- and low-pressure sodium lamps. High-pressure sodium lamps emit about 95 lumens a watt and give off an orange light. A 100-watt high-pressure sodium lamp can provide 2.5 times more light than a 100-watt mercury vapor lamp while using significantly less energy. High-pressure sodium lamps are often used for mixed outdoor and indoor lighting applications. Low-pressure sodium lamps are the most efficient HID light source, but produce a poor color of light.
Low-pressure sodium lamps are often used for outdoor security lighting.
Lighting efficiency measures
Replacing inefficient light sources with an appropriate and higher-efficiency light can result in better task lighting with energy savings that continue over the life of the lamp. Energy conservation opportunities involve changing incandescent lamps to compact fluorescents, upgrading to smaller diameter and more efficient fluorescent lamps and upgrading to HID lighting. Since lighting fixtures distribute light in different patterns, the barn layout and use should be considered in any lighting decision. Energy savings can be achieved by using simple and inexpensive technologies that go beyond lamp replacement. Some technologies incorporate programmable logic controllers and other computer-based control systems and include timers, dusk to- dawn photo controllers, half-night controllers and motion detectors. New and more efficient technologies are continually being developed.
Long-day lighting
Long-day lighting is a new development for dairy farms that involves increasing milk production by extending the day length with artificial light. According to researchers, dairy cows are day-length sensitive and can be stimulated to increase milk production by providing 16 to 18 hours of uninterrupted lighting followed by 6 to 8 hours of darkness (Sanford, 2004a). By implementing an efficient long-day lighting system, milk production can be increased by 5 to 16 per cent.
Ventilation
Proper ventilation is needed in dairy barns throughout the year to help maintain animal health and productivity, the barn’s structural integrity, milk quality and a comfortable work environment for the laborers. The air inside a barn becomes warm and humid as cows continuously produce heat and moisture. An efficient ventilation system brings fresh air that is cooler and drier into the barn, mixes and circulates it, and exhausts and dilutes moisture, dust, manure gases and odors, and airborne contaminates. Cows that are exposed to fresh air are less likely to develop heat stress, respiratory ailments, mastitis, reproductive problems and other diseases that could decrease milk production. Many dairy producers are realising the inherent benefits of a grassbased production system. Grass-based dairies utilise an ecological approach to health care by relying on natural immunity that comes with pasture access. For more information on grass-based dairying, see the ATTRA publication Dairy Production on Pasture: An Introduction to Grass-Based and Seasonal Dairying. According to experts, heat stress in dairy cows begins when surrounding temperatures exceed 65 degrees and the relative humidity is 40 per cent or higher (Ludington et al., 2004). Maintaining a healthy atmosphere by controlling mould, spores, dust and other irritants also helps reduce the chances of milk contamination and lowers health risks to the farmers. Good ventilation also reduces building deterioration due to excess moisture, which can cause rot, mildew and electrical problems.
Types of ventilation
There are two types of ventilation: natural and mechanical. Natural ventilation uses the least amount of energy and requires the exchange of air, the ability to control ventilation rates, flexibility to provide the cows a comfortable environment throughout the year and good barn construction (Wood Gay, 2002). Barns that are in the path of prevailing winds and designed with fresh air that is cooler and drier into the barn, mixes and circulates it, and exhausts and dilutes moisture, dust, manure gases and odours, and airborne contaminates.
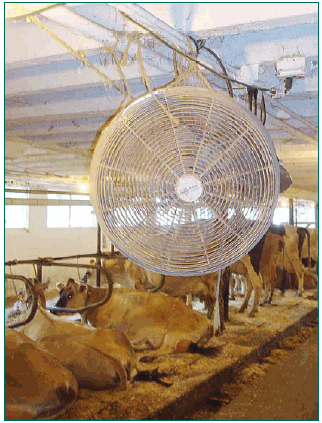
Cows that are exposed to fresh air are less likely to develop heat stress, respiratory ailments, mastitis, reproductive problems and other diseases that could decrease milk production. Many dairy producers are realising the inherent benefits of a grassbased production system. Grass-based dairies utilise an ecological approach to health care by relying on natural immunity that comes with pasture access. For more information on grass-based dairying, see the ATTRA publication Dairy Production on Pasture: An Introduction to Grass-Based and Seasonal Dairying. According to experts, heat stress in dairy cows begins when surrounding temperatures exceed 65 degrees and the relative humidity is 40 per cent or higher (Ludington et al., 2004). Maintaining a healthy atmosphere by controlling mold, spores, dust and other irritants also helps reduce the chances of milk contamination and lowers health risks to the farmers. Good ventilation also reduces building deterioration due to excess moisture, which can cause rot, mildew and electrical problems.
Types of ventilation
There are two types of ventilation: natural and mechanical. Natural ventilation uses the least amount of energy and requires the exchange of air, the ability to control ventilation rates, flexibility to provide the cows a comfortable environment throughout the year and good barn construction (Wood Gay, 2002). Barns that are in the path of prevailing winds and designed with adjustable side and end walls can take advantage of breezes and thermal buoyancy and minimise unexpected air exchanges.
Mechanically ventilated barns require air inlets and exhaust fans opposite one another. Exhaust fans are powered by an electric motor and contain hoods, protective screens and louvers or shutters. Each fan targets a certain area to provide uniform control of moisture and gases (Peterson, 2008). Ventilation fans used in livestock buildings are typically axial flow fans, which are designed to let air pass straight through the fan parallel to the fan blade drive shaft (Arnold and Veenhuizen, 1994). Traditional ventilation systems are designed with air inlets and exhaust fans placed on opposite ends of a building, whereas air inlets and exhaust fans in a cross-ventilation system are located on opposite sides of a building.
Fan selection
A properly designed and sized ventilation fan system should provide the required amounts of ventilation needed to maintain a comfortable environment for the cows and the laborers during each season. The blade sTheze and shape, fan speed in terms of revolutions per minute (rpm), motor horsepower and housing design determine how much air a fan can move. This is known as fan capacity and is measured cubic feet per minute (cfm). The size of ventilation system needed depends on its capacity to remove excess moisture during the milder and colder months of the year while forcing cool air through the building during the summer to reduce animal heat stress. Exhaust fans range in size from 5 inches in diameter to 72 inches. Exhaust fan motors may be as small as 1/20 horsepower and may exceed more than 50 horsepower (NFEC). Static pressure is the difference in pressure between inside and outside of a building, ventilation fan or air inlet (Ludington et al., 2004). It is measured in inches of water or inches of mercury. The static pressure of an efficient exhaust fan should be between 0.05 and .125 inches of water and is measured with a manometer.
Circulation fans
Circulation fans are mounted inside buildings to help improve air movement and to reduce dead air spots. There are different types of circulation fans, all of which have propeller blades attached directly to a motor or to a motor-and-belt drive system. Two common types of circulator fans used in dairy housing systems are box fans and high-volume low-speed fans (HVLS). Boxtype fans generally operate at moderate to high levels of efficiency, depending on the fan diameter, with the larger diameters being more efficient (Sanford, 2004d).
HVLS fans are large-diameter circulation fans with diameters ranging from 8 to 24 feet. One 24-foot HVLS fan can move the same amount of air as six 48-inch high-speed box fans and can save up to 3.3 kilowatts in an hour of operation (Sanford, 2004d). HVLS fans save energy by replacing existing circulation fans that are not efficient. In addition, HVLS fans tend to be quiet, reduce moisture in buildings and reduce fly and bird populations in barns.
Fan ratings
The Air Movement and Control Association International (AMCA) is an independent testing laboratory that rates fans on their ability to move air. Fans that meet certain AMCA or other reliable testing performance criteria receive a certified rating seal of approval. Th is rating can be helpful to select the proper fan for an intended use. For more information on the AMCA, visit their Web site at www.amca.org. The Bioenvironmental and Structural System (BESS) Laboratory provides research, product testing and education on agricultural fans. Performance test results are available on their Web site at www.bess.uiuc.edu.
Ventilation control systems
The use of thermostats to control ventilation systems reduces energy consumption by having the fans operate only when needed. Properly located thermostats should accurately reflect the average temperature inside the building. Mounting a thermostat at least 10 feet from a fan and at least 1 foot below the ceiling reduces the thermostat’s exposure to adverse factors, such as sunlight and air intake drafts, that can alter the thermostat’s temperature reading (Wells, 1990). All control systems should be located so they cannot be bumped by the livestock.

Timer controls and moisture sensors can also be used to control ventilation rates. However, the use of these control devices may not save energy. Timer controls cycle motors on and off to meet set ventilation rates and may use more energy to start the motors from the off mode. Timer controls also create larger temperature swings. Furthermore, moisture sensors have been reported not to work adequately in barns (Wells, 1990).
Ventilation system maintenance
Dairy ventilation systems require routine maintenance to keep fans operating at high performance levels. Poorly maintained fans and obstruction to air inlets and fan outlets can reduce fan efficiency by as much as 40 to 50 per cent. Cleaning fan parts, lubricating bearings and other moving parts, checking belt tension and alignment and removing any obstructions will keep fans performing at peak efficiency and reduce energy costs. Long-term efficiency can be improved by repairing or replacing bent, damaged or misaligned fan blades, shutters, guards and other fan parts. An air velocity meter can be used to detect reductions in the performance of the ventilation system. Control systems should be cleaned regularly and thermostats should be checked yearly for accuracy by comparing their readings against a mercury thermometer.
Factors that affect the efficiency of a livestock ventilation system
- Ventilation system design
- Fan blade type and design
- Efficiency of electric motors to power fans
- Use of fan control system
- Routine maintenance and cleaning.
Farm energy audits
A farm energy audit is a tool to help agricultural producers conserve energy and save money by implementing energy efficient equipment. The audit collects and analyses information on farm energy consumption and its associated costs, and then makes recommendations on ways to reduce them. Farm energy audits also explore ways to capture renewable energy resources that are available on a farm. Dairy operations are often good candidates for farm energy audits as there are significant opportunities for dairies to save energy and money through conservation and efficiency measures. Farm energy audits can be conducted by a professional or through do-it-yourself energy efficiency calculators. For more information on energy audits and farm energy calculators, see the ATTRA publication Farm Energy Calculators: Tools for Saving Money on the Farm.
Financial incentives
There are several federal, state and nonprofit grant and incentive programs for implementing energy efficiency and renewable energy systems on dairy farms. For information on state and federal incentives, see the Database of State Incentives for Renewables and Efficiency (DSIRE) at www.dsireusa.org.
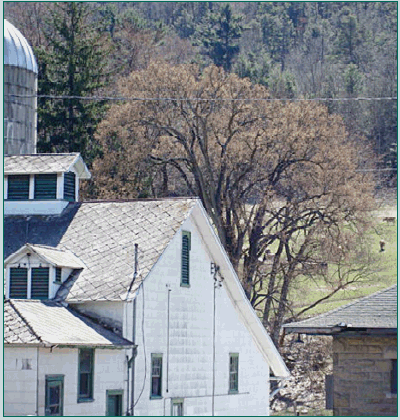
Summary
There are many opportunities for dairy farms to reduce their electrical energy consumption. Dairy farms can become more energy efficient by upgrading older equipment, installing new technologies and changing management practices for milk harvesting, milk cooling and storing, ventilation and lighting. An energy audit can be a valuable tool to a dairy farmer who is trying to understand how energy is currently being used on the farm and identify cost-saving opportunities.
April 2010