AD - Providing an Income and Answering Environment Problems
For South East England dairy farmer Gwyn Jones, the question of what to do with the manure and slurry from his 750 head herd could have been a problem, writes TheCattleSite senior editor, Chris Harris.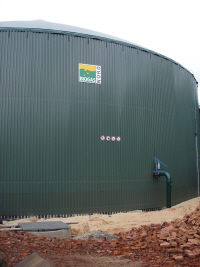
The farm in the middle of the West Sussex countryside is in a Nitrate Vulnerable Zone and new restrictions would have meant the provision of extra storage for the waste and a headache in ways of disposal.
However, Mr Jones has invested in an anaerobic digestion system to produce energy for the farm and at the same time handle the waste products from his herd.
Now, through the system that is just about to come on line, Mr Jones can produce a solid fertiliser that can go on fields for maize crops that also help to feed the digester and he can use the slurry on the fields for the grass for his herd.
By being able to use the waste products in the form of a digestate, Mr Jones estimates that he will cut his fertiliser bills by up to 50 per cent.
The biogas power plant also acts as an alternative source of income as he has been able to connect up to the local electricity substation and feed the excess power back into the grid.
The project that has taken a year to plan and get near to completion has cost about £2 million and the connection feed to the local substation put another £40,000 onto the costs. However, with the payment for the electricity fed back to the grid, plus the savings on fertiliser together with eh all important Renewable Energy Certificate payments from the government, Mr Jones sees that this will be another economic string to his business.
"The Renewable Energy Certificates were not going through when we started, but without the ROC we would not be able to make any money," said Mr Jones.
In setting up the AD plant, Mr Jones admitted that he could have applied for grants to help with the cost, but he was concerned that this could slow down the progress of the project and it could have placed restrictions on the design and the construction he wanted.
He said that going through the planning stage with the local council could also have presented problems and could become a barrier for others who wanted to follow his lead, but the fact that his farm is in a Nitrate Vulnerable Zone, made the process easier.
"I had applied for planning permission to replace a slurry tower and then because of the NVZ, I had to apply for a second tower," he said.
"It was then I decided to go for anaerobic digestion."
He said one problem that he could have faced was the council taking the view that he was processing waste - which comes under different regulations from on-farm anaerobic digestion.
However, Mr Jones said the problem was solved because he is not bringing anything else on to the farm and only using slurry, muck, grass and maize as a feedstock. The maize is taken from 300 acres he has planted and the grass from the third and fourth cuts of silage.
He says he adds the grass and maize because the slurry and muck alone do not give much gas.
At present there are two towers on the farm feeding the AD system. One tower takes 80 per cent of the production of gas while the second which he is building up in productivity has just 20 per cent.
For the anaerobic digestion to be successful and for the maximum amount of gas to be produced the towers have to be heated to blood temperature gradually by one degree a day.
Initially the gas has been burnt off until the system reaches full production potential.
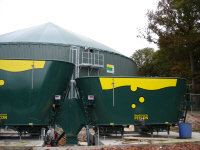
The slurry and manure is fed into the towers and through Peecon feeders. The system takes 50 tonnes of material into the towers and 50 tonnes into the separation units. Computer controlled choppers within the towers turn the mix and with the heat the gas is produced.
The whole process is automated and operated by one person.
The gas is retrieved from the digesters though a series of underground pipes and is passed through cleaners before it is burnt in the generator to produce the electricity. The engine will be running for more than 8,500 hours a year and it has a life expectancy of about five years, when it will probably have to be changed.
The electricity has been sold to Scottish Power, which has a meter on site to measure the amount the plant is feeding back into the grid. At present Mr Jones expects to be paid about 7p per watt for the electricity.
Much of the heat that is produced is used in the plant, but a lot is wasted and cannot be recycled or used.
It is estimated the plant produces enough heat to heat 20 to 30 acres or glad houses, but the cost of the insulated piping necessary to convey the heat is prohibitive, and so the heat is lost.
The whole system, that is being installed by Biogas Nord it expected to take another couple of months to be fully operational but when it is Mr Jones expects to se a new revenue stream to his farm.
November 2009